Aluminum radiused U tubes are used in a variety of industrial and commercial applications, where they help to transfer fluids or gases between different parts of a system. The curved shape of the tube helps to reduce pressure drop and turbulence, which makes the transfer of fluids more efficient. In this article, we will take a closer look at the fabrication process of aluminum radiused U tubes.
Tube Bending
The first step in the fabrication of aluminum radiused U tubes is tube bending. This process involves using a bending machine to bend the straight aluminum tube into a U-shape. The machine applies force to the tube at the desired location, which causes the tube to bend into the desired shape.
The tube bending process is critical to the fabrication of aluminum radiused U tubes, as it determines the degree of curvature and the radius of the bend. These factors are important, as they determine the efficiency of the tube in transferring fluids or gases through a system.
Cutting and Welding
Once the tube has been bent into the desired shape, it must be cut to the appropriate length. This is typically done using a cutting machine, which cuts the tube to the desired length with a high degree of accuracy.
After the tube has been cut, it may be necessary to weld the two ends of the tube together to form a continuous U-shape. This is typically done using a welding machine, which applies heat and pressure to fuse the two ends of the tube together. The welding process is critical to the strength and durability of the tube, as a weak weld can compromise the integrity of the tube and cause leaks.
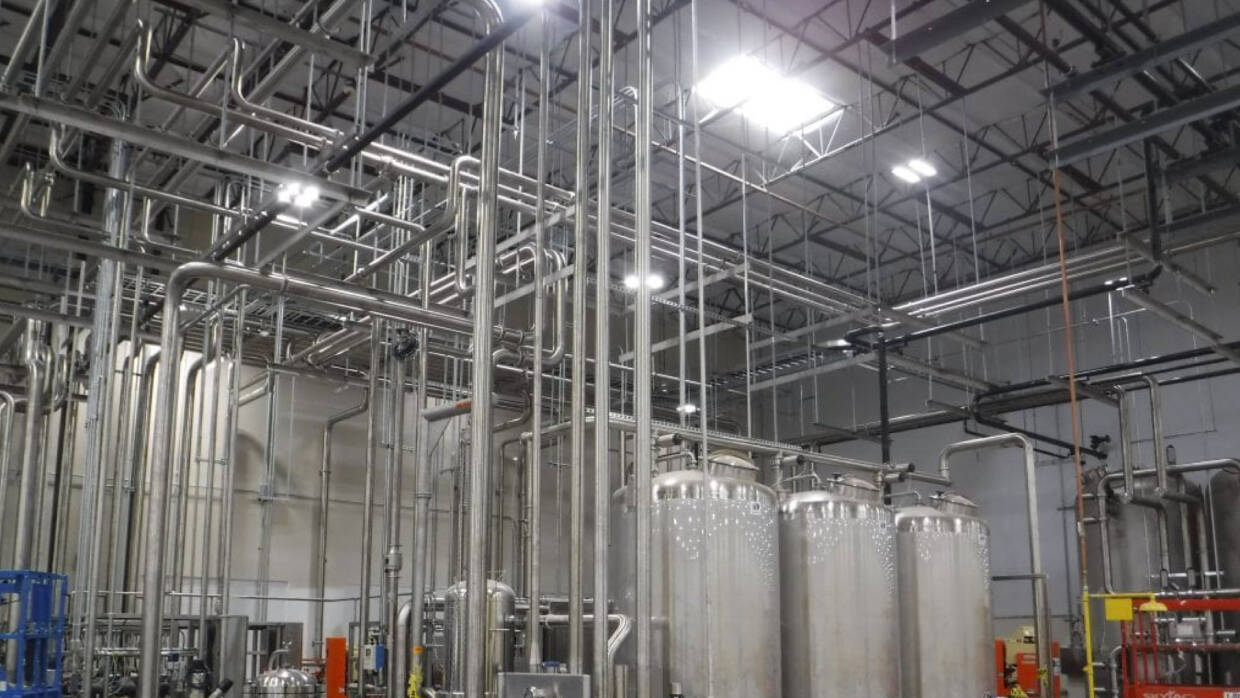
Finishing
Once the tube has been bent, cut, and welded, it may be necessary to perform additional finishing processes to prepare the tube for use in a system. This may include cleaning the tube to remove any debris or contaminants, or coating the tube with a protective finish to enhance its resistance to corrosion.
Quality Control
Throughout the fabrication process, it is important to maintain strict quality control standards to ensure that the final product meets the necessary specifications and requirements. This may involve using advanced testing equipment to verify the dimensions, strength, and integrity of the tube, or performing visual inspections to detect any defects or imperfections.
Conclusion
The fabrication of aluminum radiused U tubes is a complex process that involves multiple steps and requires a high degree of precision and accuracy. From tube bending and cutting to welding and finishing, every step must be carefully executed to ensure that the final product is of the highest quality and meets the necessary specifications and requirements. With the right fabrication techniques and quality control processes, aluminum radiused U tubes can be a reliable and efficient solution for the transfer of fluids or gases in a variety of industrial and commercial applications.